Japanese designers have created what they claim to be the world’s first viable 3D printed road bike.
The DFM01 Ouisa started as an experimental project by Triple Bottom Line design studio and then DMM.make AKIBA, a hardware manufacturing space in Tokyo, joined to provide support.

Sections of the frame are made from titanium using selective laser sintering (SLS). Essentially, this means that a laser is used to form a metal structure from powdered material.
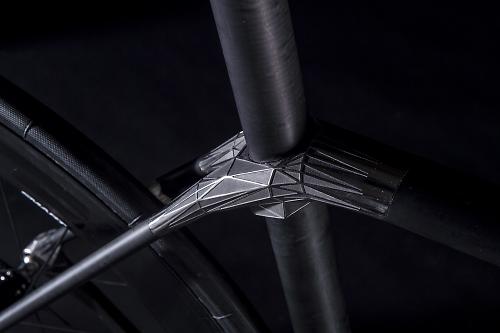
“As you can see DFM01 consists of several parts,” says Triple Bottom Line’s Satoshi Yanagisawa. “The head, seat cluster (we called junction) and entire bottom section (bottom bracket, chainstay, and lower seatstay bracket) are made from SLS titanium. Other parts (top, bottom tube and both seatstays) are market available conventional carbon tube.”

The DFM01 can be customised for each individual rider.
“This is a key factor of this frame,” says Satoshi Yanagisawa. “Basically, our geometry generating system, currently under development, allows us to create a perfectly optimized frame geometry from an individual user's information (height, arm and leg length, flexibility, and so on). The system takes those numbers then creates optimised 3D geometry. Obviously, the majority of bike manufacturers are doing this phase – creating different frame geometries – by hand at the moment.”
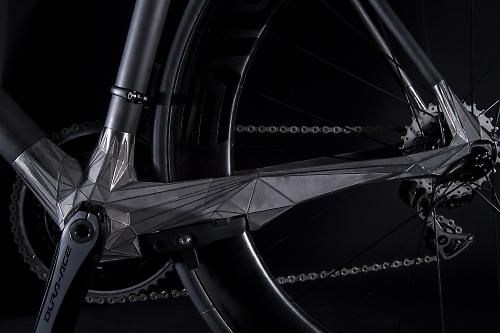
This is the first prototype of the DFM01 and the designers say that the complete bike weighs about 7kg when fitted with high-end components like a Shimano Dura-Ace groupset, a fork, bar, stem and wheels from Enve, a Ritchey seatmast on top of an integrated seatpost, and a Fizik Arione saddle.
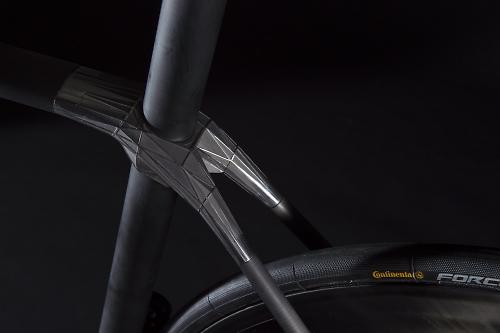
The designers are currently assessing the exact lifespan of the finished product with a view to making the DFM01 available to the public. There’s no timescale for that yet, nor any price set.
Triple Bottom Line plan to bring the DFM01 to the London Design Festival this September.
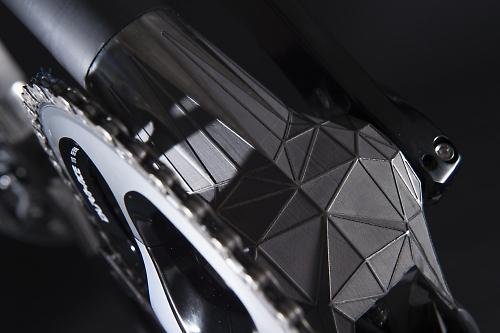
3D printing has been used in bicycle manufacture for a while now. We showed you a video of Charge 3D printing titanium dropouts a couple of years ago, for example.
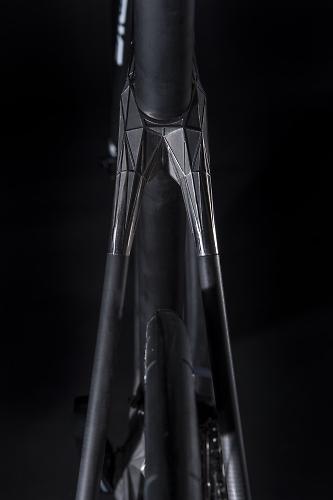
However, when engineering students at Carleton University in Ottawa, Canada, showed their 3D-printed bike earlier this year, it immediately failed thanks to a part that should have been solid having been made hollow.
For more info head over to www.triplebottomline.cc.
Add new comment
6 comments
Well, I like it...
What's the point in 3D printing when you're just making the same stuff we've been making with existing technology for years, where the benefit from having a bottom bracket printed and looking like A still from Lawnmower Man. Can't wait for the 3D printing fad to go away.
The engineering benefit is simple. It's often the cheapest way to make something in limited production sizes, replacing multiple machines and manufacturing steps. It's also used to reduce weight and increase the strength of parts, through the use of shapes and hollow spaces which are otherwise impossible to make. Laser sintering produces very strong parts, there are aerospace companies making jet and rocket engine components using it.
No idea why this is so ugly, other than it was an engineering exercise rather than a commercial part.
3D printing is about as likely to go away as the loom.
It looks to me like they've deliberately created an aesthetic that suggests that an other-than-normal manufacturing method has been used. Once that fad goes away 3D printing will be very useful for bikes.
3D printing has huge potential in bike building. Parts can be incredibly intricate without increasing cost. Maybe in the future this intricacy will be on the inside of frames, with the outside smooth and aerodynamic.
Nice, really interested to see where this sort of thing will go in the future, I think more and more SLS manufactured components could be in the pipeline